Onsite Granite Cutting: An Introduction to Quality and Efficient Stone Cutting
Granite is one of the most popular materials for countertops, vanities, and other high-end surfaces. A beautiful and naturally durable stone, granite is a preferred choice for creating elegant and long-lasting finishes in both residential and commercial settings.
However, granite can be a challenging material to work with given its density and hardness. Proper cutting tools and techniques are essential to achieving a clean and precise cut without damaging the material. This is where onsite granite cutting comes in – a solution that allows for quality and efficient stone cutting at the job site.
The Benefits of Onsite Granite Cutting
Onsite granite cutting is a process that involves cutting and shaping granite at the job site instead of cutting it in a workshop and transporting it to the location. This process has several benefits, including:
Reduced Transportation Costs and Risks
Onsite granite cutting eliminates the need for transporting heavy and fragile slabs, reducing transportation costs and risks of damage during transportation. This makes the process more cost-effective and efficient.
Customization Options
Onsite granite cutting allows for greater customization options as the stone can be cut and shaped to fit the exact specifications of the project, encouraging creativity in design and ensuring a perfect fit.
Efficient and Fast
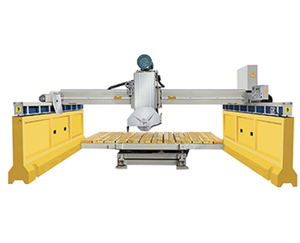
Onsite granite cutting is more efficient and faster than cutting the stone at a workshop since it eliminates the need for transportation and allows the fabricator to have direct access to the job site. This allows for a faster turnaround time and saves on labor costs.
The Process of Onsite Granite Cutting
The process of onsite granite cutting involves the following steps:
Step 1: Initial Assessment and Planning
The first step in onsite granite cutting is an initial assessment of the job site and the requirements of the project. This includes determining the dimensions and angles of the cut, the thickness of the slab, and any special requirements such as bevel edges or curves.
Step 2: Preparing the Work Area
The work area is then prepared, which involves setting up the equipment, such as diamond saw blades and polishing pads, and ensuring that the area is safe and free of dust.
Step 3: Cutting and Shaping
The granite is then cut and shaped using specialized tools and machinery, including diamond saw blades and polishing pads. This process requires a high level of skill and expertise to ensure a precise and smooth finish.
Step 4: Finishing and Cleanup
The final stage of the process involves finishing and cleaning up the work area. The granite is polished to a smooth finish, and any residual dust or debris is removed.
The Importance of Choosing a Professional Fabricator
Choosing a professional fabricator for onsite granite cutting is crucial to achieving quality and efficient results. A professional fabricator will have the necessary expertise, experience, and equipment to cut and shape granite to the exact specifications of the project while ensuring a smooth and precise finish.
It is important to research and choose a fabricator who has a good reputation, a portfolio of work, and positive customer reviews. This will ensure that the onsite granite cutting process is carried out efficiently, with the highest level of quality and customer satisfaction.
Conclusion
Onsite granite cutting is a valuable and efficient process that allows for quality and precision in stone cutting. It offers several benefits, including reduced transportation costs, customization options, and faster turnaround times. Choosing a professional fabricator for onsite granite cutting is crucial to achieving quality and efficient results in any project that requires custom cut and shaped granite.