Best Diamond Hole Saw For Granite will develop in the direction of diversification, high efficiency, precision, automation and assembly line in the future.
Stone mining machinery such as Best Diamond Hole Saw For Granite, large mast cranes, multi-head drilling rigs, etc. adapt to the direction of increasing production efficiency of modern stone blocks; stone processing machinery develops towards continuous production lines; large sand saws, frame saws, multi-knife cutting machines , continuous mills and surface treatment equipment, special-shaped processing machines, engraving machines, processing centers, etc. will all be favored by users; decoration machinery is showing a trend of miniaturization, portability, and diversification;
Stone maintenance machinery is developing toward miniaturization, specialization, high efficiency, and portability; stone testing instruments and equipment are developing toward more specialization, standardization, generalization, miniaturization, and intelligence; stone decoration design is toward computers and databases. , Network development; the combination of corresponding equipment, instruments and technology will also be an important part of the development of stone software science in the future.
[caption id="attachment_120" align="alignnone" width="600"]
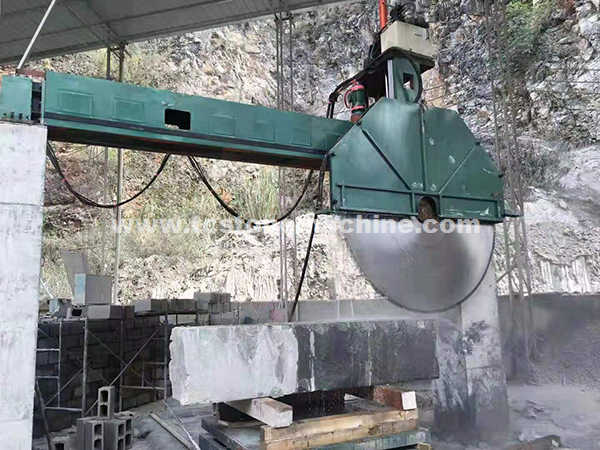
Best Diamond Hole Saw For Granite[/caption]
Common wear forms of Best Diamond Hole Saw For Granite are as follows
(1) Abrasive or hard particle wear
This kind of wear will often occur in the boundary friction and mixed friction state. The abrasives (or hard particles) between the relatively sliding friction pairs mainly come from: the high points of the uneven friction surface in the microscopic state, which are sheared and left on the friction surface during the relative motion of Best Diamond Hole Saw For Granite Between, as the lubricating oil enters the hard particles between the surfaces of the guide rail; due to poor protection, the chip particles falling on the guide rail surface enter between the friction pairs, and the force of the particles between the friction pairs can be decomposed into Two component forces perpendicular to the friction surface and along the direction of movement of the friction surface, the vertical component force will press the abrasive to the metal surface, the greater the force and the harder the abrasive grain, the deeper it will be pressed; the component force along the friction surface will be Make the abrasive grains slide relative to the metal surface, "cut" the guide rail surface, and cause "scratches" or "grooves" on the friction surface. The higher the hardness of the abrasive, the greater the relative sliding velocity, the greater the pressure, and the greater the damage to the friction pair. Abrasive wear is inevitable and can only be minimized. Therefore, the hardness of the supporting rail should be increased as much as possible during design, and the value of P*V (product of pressure and velocity) should not exceed the allowable value of the material.
(2) Adhesive wear or galling
Adhesive wear is also called molecule-Best Diamond Hole Saw For Granite mechanical wear. When two friction surfaces are in contact with each other, the material undergoes plastic deformation under high pressure, and the friction during relative motion destroys the oxide film on the surface layer. Mutual attraction and penetration between molecules will occur between the newly exposed metal surfaces, so that the contact points will bond and bite welding will occur. The relative movement of the contact surface will pull the solder joint apart, causing tearing damage. Bite welding is not allowed. In order to avoid this situation, in addition to the correct selection of materials, hardness and maximum pressure control, the plane error, surface roughness or number of contact points of the sliding surface must also be correctly specified during design.